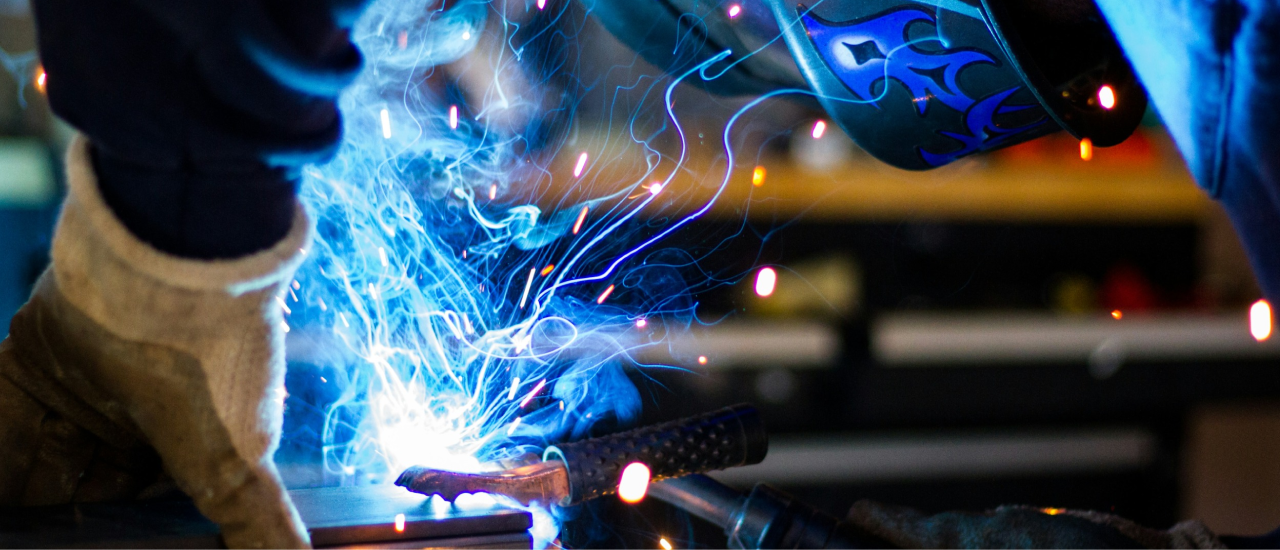
Melt Metal, Make Masterpieces
Equip yourself with the best gear to shape metal into masterpieces, showcasing your expert craftsmanship.
You’re attempting to view exclusive content only for members in the __tier_name__.
Already have an account? Sign in
You’re attempting to view exclusive content only for members in the __tier_name__.
Already have an account? Sign in
You’re attempting to view exclusive content only for members in the __tier_name__.
Already have an account? Sign in
You’re attempting to view exclusive content only for members in the __tier_name__.
Already have an account? Sign in
SKU:ED037254
Brand:Lincoln Electric
Lincoln LINCORE 55 is low alloy steels designed for rebuilding of carbon or low alloy parts used in Metal-to-Metal wear applications, works best in non-lubricated rolling or sliding.
Enhance Your Gear With Accessories
Lincoln Lincore® 55 Flux-Cored MIG Welding Wire - 10lb Spool (ED037254)
Ideal for building up on carbon and low alloy steels. Use as an underbase for carbon steel parts prior to hardfacing. Great compressive strength under heavy loading. Deposits are generally crack free, machinable and can be flame cut. Deposit thickness is unlimited. Used in Metal-to-Metal wear applications, works best in non-lubricated rolling or sliding.
Note |
---|
Cold parts should be warmed to at least 25°C (75°F). Higher preheat of 150 - 260°C (300 - 500°F) may be necessary on thick parts or heavy sections. |
Interpass temperatures between 150°C (300°F) and 200°C (400°F) do not affect the hardness of Lincore® 55 significantly. |
Classification | Number of layer | Hardness Rockwell C |
---|---|---|
Typical Result | 1 Layer | 50-59 |
Typical Result | 2 Layers | 50-60 |
Typical Result, Work-hardened | 1 Layer | 53-62 |
Typical Result, Work-hardened | 2 Layers | 56-62 |
Typical Result, Flame-hardened | 2 Layers | 52-54 |
Typical Result, 180°C (350°F) Interpass Temp | 1 Layer | 50-55 |
Typical Result, 180°C (350°F) Interpass Temp | 2 Layers | 55-59 |
Classification | Product Size | %Al | %C | %Cr | %Mn | %Mo | %P | %S | %Si |
---|---|---|---|---|---|---|---|---|---|
Typical Result | .045" (1.1 mm) | 1.4 | 0.45 | 5.3 | 1.3 | 0.8 | 0.010 | 0.004 | 0.53 |
Typical Result | 1/16" (1.6 mm) | 1.4 | 0.45 | 5.3 | 1.3 | 0.8 | 0.010 | 0.004 | 0.53 |
Typical Result | 5/64" (2.0 mm) | 1.4 | 0.45 | 5.3 | 1.4 | 0.8 | 0.010 | 0.004 | 0.60 |
Typical Result | 7/64" (2.8 mm) | 1.4 | 0.45 | 5.3 | 1.4 | 0.8 | 0.010 | 0.004 | 0.60 |
Diameter | Polarity |
ESO
mm (in.) |
Wire Feed Speed
m/min (in/min) |
Voltage
volts |
Approx. Current
amps |
Deposition Rate
kg/hr (lb/hr) |
---|---|---|---|---|---|---|
0.045 in (1.1 mm) | DC+ | 45 (1 3/4) | 5.1 (200) | 25 | 85 | 1.6 (3.6) |
0.045 in (1.1 mm) | DC+ | 45 (1 3/4) | 8.9 (350) | 28 | 125 | 3.0 (6.6) |
0.045 in (1.1 mm) | DC+ | 45 (1 3/4) | 12.7 (500) | 31 | 165 | 4.3 (9.4) |
1/16 in (1.6 mm) | DC+ | 45 (1 3/4) | 3.8 (150) | 26 | 125 | 2.2 (4.8) |
1/16 in (1.6 mm) | DC+ | 45 (1 3/4) | 6.4 (250) | 29 | 195 | 3.8 (8.4) |
1/16 in (1.6 mm) | DC+ | 45 (1 3/4) | 8.9 (350) | 32 | 245 | 5.5 (12.1) |
5/64 in (2.0 mm) | DC+ | 45 (1 3/4) | 3.2 (125) | 24 | 190 | 3.2 (7.0) |
5/64 in (2.0 mm) | DC+ | 45 (1 3/4) | 5.1 (200) | 27 | 295 | 5.0 (11.0) |
5/64 in (2.0 mm) | DC+ | 45 (1 3/4) | 6.4 (250) | 30 | 330 | 6.2 (13.7) |
7/64 in (2.8 mm) | DC+ | 64 (2 1/2) | 2.3 (90) | 25 | 280 | 3.8 (8.4) |
7/64 in (2.8 mm) | DC+ | 64 (2 1/2) | 3.2 (125) | 27 | 350 | 5.2 (11.5) |
7/64 in (2.8 mm) | DC+ | 64 (2 1/2) | 4.4 (175) | 30 | 420 | 7.3 (16.0) |
Diameter | Polarity |
ESO
mm (in.) |
Wire Feed Speed
m/min (in/min) |
Voltage
volts |
Approx. Current
amps |
Deposition Rate
kg/hr (lb/hr) |
---|---|---|---|---|---|---|
0.045 in (1.1 mm) | DC+ | 45 (1 3/4) | 5.1 (200) | 25 | 85 | 1.6 (3.6) |
0.045 in (1.1 mm) | DC+ | 45 (1 3/4) | 8.9 (350) | 28 | 125 | 3.0 (6.6) |
0.045 in (1.1 mm) | DC+ | 45 (1 3/4) | 12.7 (500) | 31 | 165 | 4.3 (9.4) |
1/16 in (1.6 mm) | DC+ | 45 (1 3/4) | 3.8 (150) | 26 | 125 | 2.2 (4.8) |
1/16 in (1.6 mm) | DC+ | 45 (1 3/4) | 6.4 (250) | 29 | 195 | 3.8 (8.4) |
1/16 in (1.6 mm) | DC+ | 45 (1 3/4) | 8.9 (350) | 32 | 245 | 5.5 (12.1) |
5/64 in (2.0 mm) | DC+ | 45 (1 3/4) | 3.2 (125) | 24 | 190 | 3.2 (7.0) |
5/64 in (2.0 mm) | DC+ | 45 (1 3/4) | 5.1 (200) | 27 | 295 | 5.0 (11.0) |
5/64 in (2.0 mm) | DC+ | 45 (1 3/4) | 6.4 (250) | 30 | 330 | 6.2 (13.7) |
7/64 in (2.8 mm) | DC+ | 64 (2 1/2) | 2.3 (90) | 25 | 280 | 3.8 (8.4) |
7/64 in (2.8 mm) | DC+ | 64 (2 1/2) | 3.2 (125) | 27 | 350 | 5.2 (11.5) |
7/64 in (2.8 mm) | DC+ | 64 (2 1/2) | 4.4 (175) | 30 | 420 | 7.3 (16.0) |
Note |
---|
Cold parts should be warmed to at least 25°C (75°F). Higher preheat of 150 - 260°C (300 - 500°F) may be necessary on thick parts or heavy sections. |
Interpass temperatures between 150°C (300°F) and 200°C (400°F) do not affect the hardness of Lincore® 55 significantly. |